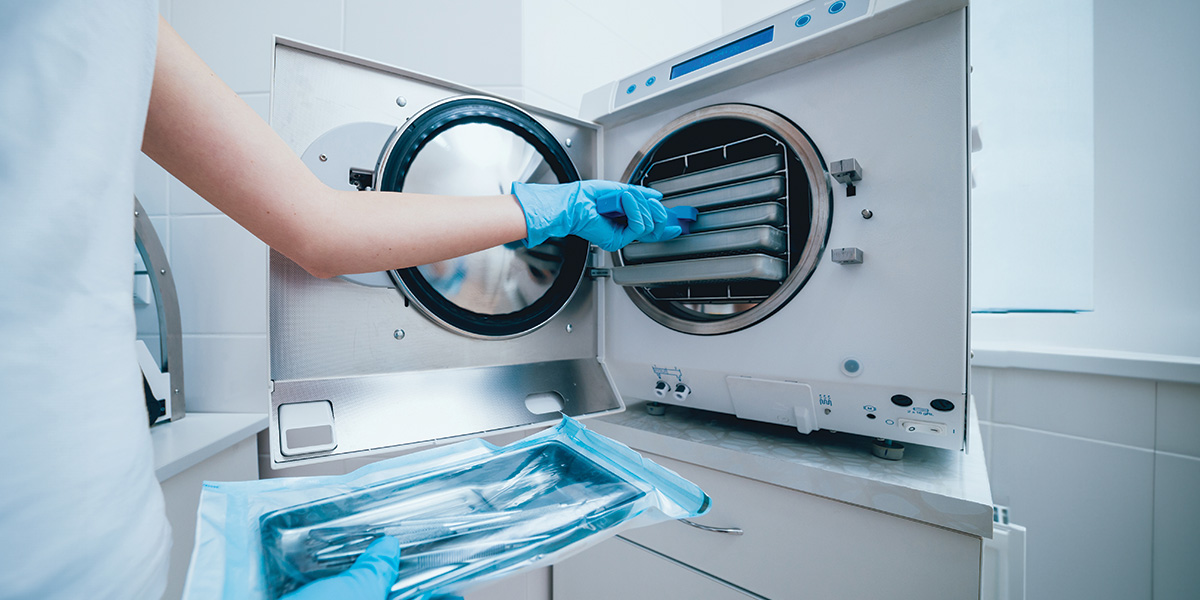
In the realm of disinfection and sterilization, precision and reliability are paramount to maintaining pristine hygienic standards. Often handling highly concentrated fluids, sanitizing equipment requires specialized pumping solutions to ensure effective and consistent results. Here's a comprehensive guide to successfully navigating the disinfection and sterilization pump selection process.
Understanding Fluid Characteristics
The first step is to understand the chemical properties of the fluids you're working with. Most cleaning solutions like hydrogen peroxide are highly concentrated, making them prone to blockages. Some like peracetic acid and acetic acid naturally off-gas, creating buildups of gas pockets that can cause incompatible pumps to seize. Many disinfection and sterilization fluids also contain aggressive chemicals, so it's crucial to choose a pump made with chemically compatible materials to avoid operational failure. Fluid Metering uses chemically inert components like ceramic pistons and cylinders, an upgraded cartridge seal design, and a special PTFE coating on the outer diameter of the piston to prevent corrosion and degradation, significantly improving pump performance and longevity. Other factors like temperature and viscosity will also come into play. While some cleaning solutions like water (1-5 CP) and isopropyl alcohol (~2 CP or less) flow easily, other liquids like glycerol (~1500 CP) have higher viscosities requiring different pump specifications.
Defining Performance Specifications
Once you've characterized the fluids, then it’s time to outline the needed performance specs. For most disinfection and sterilization applications, the pump will typically only have to handle one type of fluid: the working fluid. However, on rarer occasions, it can be necessary for it to handle one additional fluid: the flush fluid. In any case, the pump must be capable of achieving the necessary pressure (usually 50-100psi) to overcome system resistance and deliver the fluid effectively. Determining the necessary flow rate enables the pump to move the right amount of fluid within the desired time frame. This will normally vary from 1-50mL/min - a slower rate compared to other applications. Finally, a precise dosing accuracy level of about +/-1% is ideal.
As part of the specification requirements, you should also consider how the pump will fit into the existing system in terms of physical space, connections, and compatibility with current equipment to ensure seamless integration. FMI’s miniature sized OEM microfluidic pumps easily save on space and are normally driven by a stepper motor that can be controlled by a user-friendly system PLC (programmable logic controller).
Selecting the Right Pump Type
For highly concentrated cleaning fluids, positive displacement pumps are often the go-to choice. Fluid Metering offers state-of-the-art valveless piston pumps renowned for their exceptional metering precision and accuracy. These pumps maintain a steady flow rate, which are crucial requirements of medical and laboratory applications. The maintenance-free nature of these pumps sets them apart from peristaltic and syringe pumps, eliminating the need for routine cleaning or expensive maintenance post-installation. This in turn establishes a significantly lower total cost of ownership. In contrast, peristaltic pumps, which rely on tubes, require regular tube replacements due to wear and tear from compression. Such wear can lead to leakages, a notable decrease in pump accuracy, and an elevated risk of contamination as external pollutants can infiltrate through the tubing's cracks. FMI’s positive displacement pumps are engineered for longevity, capable of enduring millions of cycles and extensive operational hours. On the rare occasion that cleaning is required, a simple solvent flush will do the trick.
Expert Consultation
By carefully considering these factors, you can choose a microfluidic pump that not only meets the demands of your disinfection and sterilization equipment, but also enhances the overall efficiency and effectiveness of your operation. Whether your OEM machine will be spray-cleansing hospital rooms, disinfecting surgical tools, sterilizing dental drills, or cleaning beverage tap lines, Fluid Metering's engineer-to-engineer support team will provide valuable insight into selecting the right pump for your specific needs. Their experience and knowledge in fluidic control technologies make them an indispensable resource in your selection process. Remember, the right pump is not just a component; it's a cornerstone of your machine's success.